I studied the bbox, focbox, escape, 4.12 and they all use the same schematic in general, two shunts, DRV8302. The main difference are the FETs and the mounting and connection of the caps. There are some newer designs like Vesc 6 (trampa) using direct fets with nice housing but bad thick thermal cushions between the Fets and cool housing. I have not analysed it because its overpriced for my budget. The problem seems to be always the same:
You have an amount of electrical potentials, typically 5, which are the motor terminals and the supply voltage, ground, which must be isolated under all circumstances.
So there has to be some insulation between the cool housing and the Fets, also allowing to even out mechanical tolerances.
VESC4.12 fet https://www.infineon.com/dgdl/irfs7530-7ppbf.pdf?fileId=5546d462533600a40153563a9d1e21d8
The direct fets used are https://www.infineon.com/dgdl/irf7749l2pbf.pdf?fileId=5546d462533600a40153560445e71ca2
Later VESC design use even smaller Fets:
https://www.onsemi.com/pub/Collateral/NTMFS5C628NL-D.PDF
The original VESC 4.12 was very compact in its current paths, the high side fets, as always, share their cooling plate, the Drain, which has supply potential. Their Source is directly connected to the motor terminal and because its double sided also the low side fets drain cooling plate. The only disadvantage are the shunts, which need to be mounted on the PCB, with 1mOhm, they are a pain regarding thermal load to the PCB. The heat cannot be transferred from there. So i added some cooling where it is possible to mount without changing the layout or dissoldering the fets.
The problem is, that the PCB transferring the heat is very thin, typically 70µm, which generates heat itself. Even 105µm at 100A is too small to transfer heat in a valuable amount. At least the PCB is now cooled and sucks the heat from the Drain cooling of the fets.
The newer VESC designs all use direct fets with the promise to enhance the cooling dramatically.
Now, lets compare some aspects of the data sheets.
irfs7530 : Max R_DS_ON: 1.4mOhm at 100A ; R_JC: 0.4K/W, MaxP_D: 375W
irf7749: Max R_DS_ON: 1.5mOhm at 120A (2%Dutycycle); R_JCan: 1.2 K/W MaxP_D: 125W
NTMFS5C628: Max R_DS_ON: 2.4mOhm at 50A; R_JC: 1.3K/W; MaxP_D: 110W, two are used in parallel, so you get doubled or halved values.
The effective R_DS_ON is almost the same, although the oldest parts wins. Thermal resistance is definitely worser for the newer parts, and the elder irfs7530 can be used as a heater, it has the largest footprint.
So the newer designs have not made so much out of the benefit of direct top cooling or distributing heat over a larger area. They use a larger PCB area to accomplish the same or even worse performance.
Why is it so?
The ESK8 scene calls for very light material. They have a typical usecase: Accelerate, hold speed with low torque, decelarate. With 3kW you could accelerate to 50km/h within seconds. All the tests of the ESK8 scene are not valuable for us. The peak power demand of a skateboard is similar to the average power demand of a windsurfboard without foil. And honestly: What helps? Power!
What can be done with 4.12 derived designs?
Stabilize the voltage by more capacitors and better wiring, so there is less heat created by the leads, contacts, caps, which surround the esc. The less heat they produce, the more they can take from the PCB.
Get the heat away by air and rib cooler and spread it.
Cancel out the root cause.
What is producing the heat? The R_DS_ON for sure, the shunts, the PCB and the switching losses inside the fets, the latter one can only be changed by the gate driver concept.
Suggestions: Use 0.5mOhm shunts because it seems easy. Use fets with lower R_DS_On. I found one and bought some.
I think i will integrate it to the VESC4.12 by a copper adaptor which acts as a primary heatsink, 1-2mm thick, and as a terminal for all 5 power connections. These copper plates exceed the original PCB around 10-30mm. They can be used to mount cushions, ribbed coolers, heatpipes, watercooler, whatever, with or without insulation. By this the cooling area is multiplied and those supadupa fets can play their role out and deliver 100A continously.
Even an immersed fluid cooling would be possible.
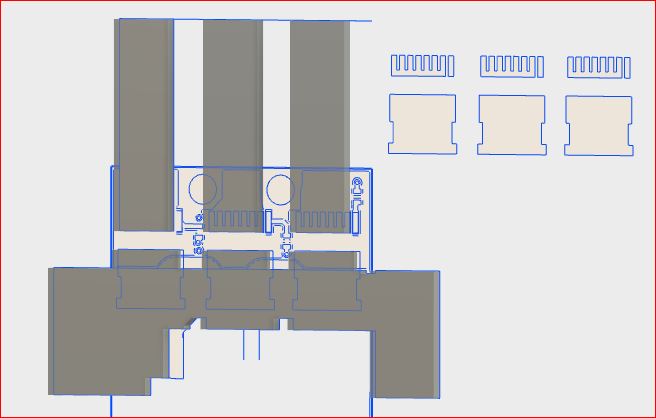
What do you think?