Progress update…
After going in circles with a 3D printed design (FD#2/underboard) - was going to use angle aluminium supports around the base plate bolts. But concerned 3d printed plastic will warp. I will loop back to this as I like the concept and it gives flexibility in design… just think I need to get something working first which is more durable and watertight, so…
Now switching to rectangle aluminium tube: 100x25x1.6. Initially will try doing this with brazed supports (10mm aluminium tube) for mast base plate bolts.
This should be similar to FD #2 Slim size. But 25mm narrower and with twice the battery capacity for only another 20mm or so in length. That’s the goal anyway 
Will have 2 x 6s2p battery packs - fore and aft giving 12s2p.
Biggest challenge will be closing the ends - making them water tight. Current plan is to make a silicone seal on flat plate ends and braze on some connector supports to the main body Any other suggestions?
Have built a test section of the 100x25 box tube. Drilled holes for the 10mm aluminium tube for the base plate bolts.
Then brazed the tubes in…
Then mounted on the board…
I think I should put some flat plate underneath to span across the outer sides of the fin boxes.
Next, need to test strength (with some dock starting) … will the brazing hold up (they need to be waterproof) and will the main box tube hold up??
Project update…
Turns out the brazing cracked under load (doing some dock-starting/pumping).
So new plan… Cast strengthened resin inside - this will encapsulate the electronics and provide strength and waterproofing for bolt holes.
Next challenge, removable waterproof ends for swapping battery mid session. Will have a 12S1P at each end of the box section (either side of the electronics/base plate).
Will use end inserts with foam rubber (EPDM 414 Supersoft self-adhesive) squashed between 2 plates using bolts to tighten (which expands the rubber to seal and hold in place).
Initially tried 1 layer of rubber but it leaked a little (through the bolt holes) so tried with 2 layers with a strip of aluminium between and using embedded threaded inserts on the inside.
The configuration is (from the inside):
-
3d printed rectangle with threaded inserts (blind to stop any chance of leaking)
-
EPDM414 (24x 6mm)
-
aluminium plate (3mm)
-
EPDM414
-
3D printed end - 4mm inserted into box section and 30mm outside to provide rounded nose/end to box section for better hydrodynamics.
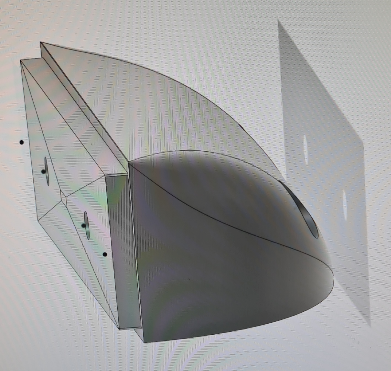
I left this in the pool for over 1/2 hour - with no sign of water ingress.
Will still add some rubber seals/washers for the bolts and maybe some teflon tape on the thread.
Have used PETG-CF - will paint this to waterproof it. Also printed it standing on end, hopefully add more waterproofing with layer direction. Could also add a layer of waterproof tape upon use as a last resort.
1 Like