I am wanting to water proof all electrical components, receiver, ESC and battery with the idea of having an underwater type setup (like FD gen2) with the electrical components in a sealed unit.
I have seen others on this forum coat circuit boards with epoxy - can this be any epoxy? Also is thermal epoxy conductive and if so there for not suitable for this?
Also need to consider heat buildup - I suspect not an issue for the RX but wondering about coating the ESC in epoxy - if I glue (thermal paste or epoxy?) the heat sink to an aluminium plate that is external (for a under board setup) - will I still have heat buildup inside that might causes issues ie if its water tight, might this blow the seal - with expanding air inside?
I was thinking I might be able to fill the electronics area with expanding/polyurethane foam/glue - insulation and waterproofing.
Even typical eg west systems Laminating epoxy can withstand 90-120deg C. Natural cure (marine) silicone typically resist 150-220 degrees. As long as the heat can escape troucgh thermal conductivity (heat sink) and no airbubbles are trapped in the process. I’ve used natural cure silicone so far no signs of deforming. Too thick normal epoxy around a battery pack requires good margin on the cells and strips used afik. The hard part with thick silicone is getting it in every small corner, try a clothing vacuum bag, works great for me in board and foil builds.
2 Likes
I have used, potting compound for total waterproof and brush on conformal coating. They are both good for electrical.
1 Like
Now looking at battery and phase connectors…
I will be using 2 x 6s2p to get 12s2p - and housing them under the board (like FD#2). Using either XT60 or XT90 for the batteries and I was hoping to have one end surface mounted/embedded in the electrics part of the assembly.
Has anyone experience embedding connectors (XT60 or XT90) in resin? I find these connectors very difficult to pull apart - so I’m concerned that they pull out of the resin as they don’t have much to grip onto.
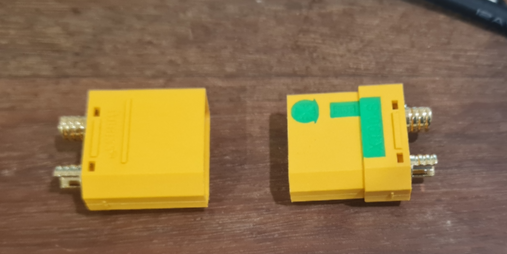
I have also bought some XT60E (surface mount with the faceplace/screw holes)
Assuming I would use threaded inserts… but again these are very hard to pull apart - concerned for pulling inserts out.
Also have same concerns with the MR60 (for phase wires) - was hoping to embed like FD does.
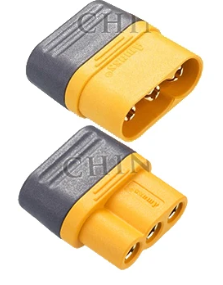
May just have to use them not attached so I can pull them apart by hand.
Also, is battery grease (like FD use) good enough to waterproof connectors like these (if they were external/under water)?
FYI - considering using the XT90 anti-spark connectors on each battery pack - as the XT60’s dont have an antispark version… that would save me having a Y harness - could just solder up that inside the electronics part.
Any suggestions?
FYI - found a solution for the stiff connectors (too hard to pull apart by hand)…
Gently squeeze the male prongs with some needle-nose pliers… just a tiny amount (a fraction of a mm) makes a huge difference. You still want a snug fit (so wont weaken connection) - this now makes it easier/possible to pull apart by hand.
This helps my design significantly as I can use the surface mount type of plug (XT90E) - so no need to additional wire length so I can reach the connectors (which were to be placed within a hard to reach cavity).
Have also learned that I need to be using XT90 connectors on my batteries. Based on what I’ve read (on RC forums) it is probably not wise to use XT60’s as I will be using two 6s packs in series (12s) - and therefore the full load going through the connectors.
Another question… if the motor is under water and therefore the phase wires… does it matter if the phase wire connectors at the mast base are not waterproof? Or are they (phase wires) waterproofed on the motor??
Please correct me if I’m wrong or have misunderstood things or if there is a better way to approach things - all questions and suggestions welcome.
1 Like