I havenât received the test unit yet. Freefly were waiting for adaptor cables. Once I have it and test it Iâll be sure to let everyone know though.
Here is some of my design:
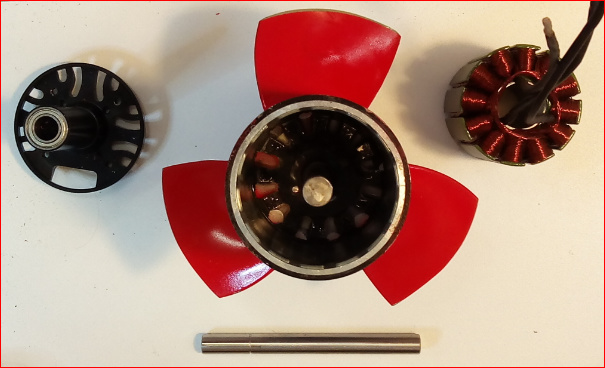
Its a APS 6384PG with a heavily cut down to 136mm OD , Yamaha 7 1/4 x 5 1/4" prop as base.
3D Printed hub which makes the streamline.
Hey @PowerGlider your motor prop combo looks slick, nice work. How would you rate the performance of the 6384 for foiling? I have one in my build and im starting to test, but so far im struggling with getting enough thrust and havenât got up on the foil yet. I guess its because its a lower power output than most motors on here so needs to be a good efficient setup to get going.
Yes, you got to find the correct pitch. At the moment i am using a 7 1/2 x 8BA which looks similar:
You can see the motor is driven with 90A constantly without damage. But the problem is it runs with around 70% Dutycycle only and the RPM is forced down to 2700RPM, so there is some potential to get higher power with less pitch.
I have 7 1/2 x 7BA which i want to try next, but there is some work to do, takes maybe 20 hours.
First i need to measure geometry, than sketch it in fusion360, print a hub for this prop. Additionally it takes hours on the lathe to rework the prop to overlap with the motor rotor.
Eventually i have to make a new motor rotor if i find it impossible to remove the 7 1/2 x 8BA from the currently used motor rotor.
Also see here: Any interest in a custom e-foil ESC? - #121 by PowerGlider - Electronics (ESC, remote, batteries) - FOIL.zone
Good to hear you have the 6384 working. Im currently working on a 170x125mm (6.7 x 4.9") 2 bladed prop generated in java prop and 3d printed. Tank testing gets 18kgs static thrust at 1500rpm and 70A of motor current. I need to tweek a few limits in the vesc to increase things. I will take this setup for sea trials, but i can see the next step is probably a lower drag prop to get the rpm and power up similar to what youâre producing.
So currently it is being maintained Meaning: I got some fotos for you!
Stainless Bearings look awful and are swapped by ceramic hybrid. They still work somehow.
Circlip broke when i tried to remove it! Its not stainless.
The grease reservoir is gone, only some brown substance is over. The rusting circlip spreaded everywhere.
I had 4 stainless screws holding the prop. The aluminium corroded and it was large pain to remove them. One broke off and cannot be removed. Now i will use 2 threaded stubs and nuts, so the stubs can stay where they are.
I got sand and stones through the motor during this incident last summer, where it drove into the sand bank with full power and speed. There are lots of scratches on the stator and rotor. The rotor did not suffer too much, the stator has some small stains where the epoxy was removed, nothing dramatical.
Some History:
Stator built in March 2018, was used in mediterrenean sea and south england and again mediterranian salt water. Also tested some times in fresh water in germany. All together around 30-40 hours. The bearings are even older.
The first prop motor rotor had too little pitch 5" and was swapped to 8" which seems too much.
Now i build the 3rd prop for this setup with 7".
I cut them down to 136mm.
I think with every mm more diameter you get more bollard thrust. When end speed matters, medium diameter is better.
My very first build from 2016 was around 170mm. It has lots of thrust, towing another surfboard is not problem, but end speed was not gliding and too high power consumption.
Something between 120 and 170 is good, depending on power and speed. A Surfboard needs 2-3 kW to glide in rough waters and windy conditions.
I also experimented with the angle of attack of the complete fin. Since a while i angle it down by 7°. This lifts my stern up. I wonder if one could build a hybrid foil, with a lifting stern foil and two pawnsâŠ
Back to reality⊠I am writing from remote location, so different user as i have no access to my usual computer.
I would like to discuss the aspect of energy consumption versus speed. This is a different surfboard but the rest of my setup is the same.
Please note: This whole thread is about a gliding surfboard, there is no foil. There was some discussion in the forum about the power consumption regarding transition from displacement to glide ride. Here are some facts:
Raw data was taken from straight ride sections:
EDIT on behalf of XSailor request below:
Slow speed data added:
From raw data:
5km/h seems to be impossible to record under steady conditions, the power consumption is such low i cannot dial it in with my remote without reprogramming the VESC. Also wind, current and waves and also holding the course is becoming difficult.
Thanks for good data. I was the guilty one talking about transition from displacement to glide ride:) Generally speaking that is a well known phenomena. When a planning hull do the transition from max hull speed to planning, there is an transition phase where economy is incredibly bad until the hull starts to plan properly. On a proper surfboard that happens probably at a very low speed, guess hull speed i type 3 knots only. I have in this size boat size only a SUP without motor(so far) so donât yet have much practical experience. A surfboard is very narrow in relation to the length so that also softens the impact, narrow hulls might even lack totally the âsemi planningâ stage thus a linear curve is possible.
One thing (again not 100% sure if it works on surfboards) at higher speeds a wide but short surface against water is more economical than long an narrow. This is due to wet surface area. So at least in theory a shorter but wider surf board would achieve better W/h/km. In reality think we need to have higher speeds than above to take full benefit of this.
If You have the time, test for a few minutes to do like 5 kmh to se the power consumption. In theory it should be better than the linear curve would suggest, but that is only theory, not sure how the ESC efficiency would be affect such low power?
Length is much better for speed when it comes to boats and surfboards. Thereâs a reason k1 kayaks, surf skis, big wave surfboards and the like are all very long! To speed up short, wide boards you reduce the rocker on a surfboard. Rocker and rail profiles have a huge amount to play in how the water release off a board.
A shorter, wider board becomes easier to turn though. So what you want is the happy compromise.
Is the shape of a surfboard is appropriated to go fast on a » flat » « none moving » water?
On a general level, Yes and No about the length. It matters are we talking about a displacement hull or planning hull. A kayak moves with a small engine effortlessly rather fast(a longer kayak will be faster than a short), but at a certain speed it starts to bury its stern deep and no increase in speed. So a 5 hp outboard moves faster on a short, wider (and light ) flat bottom boat than on a kayak. But before the flat bottom is on plane, it is really slow and has much higher drag than the kayak. Very much simplified, for planing hulls it is basically not about the length of the boat but the wetted surface. For displacement huls the length is a major factor, not to forget the lenght / beam relation,
A surfboard is little odd animal. It has to have small drag in low speed but also be capable of high speed, so it is a compromises design speed wise. Then there is also the sea keeping aspect. A wider hull is much worse in higher speed for bottom slamming so it can not be very wide either.
For motorized surfboard, not sure optimal design is out there ye, design will also be different based on speed range. Technically it is a small, planning motorboat so minimal wetted surface is one goal to get good efficiency. But there are many other aspects to it also so its not clear.
There is no yes and no. A longer hull will be faster unless the motor in insufficient to drive it properly based on the crafts weight. Power boats are not short and fat. Submarines are not short and fat. High speed jets are not short and fat. Land speed cars are again not short and fat. They are all shaped like needles. What slows water based craft down is the rocker profile and and rail profiles.
I have built boats, designed and built surfboards.
All big wave surfboards are long for a reason. Then if you move into the realms of the tow surfboards, they are short, but never fat. They are always thinner than standard boards.
You are welcome to show an example where you believe this is not the case.
There is always a Yes and No, especially in hull design:) I donât see where we disagree that much?
For displacement huls i have all time said that narrow long is good as also not to forget the beam length ratio(narrow is better for speed). For displacement boats there is something called hull speed, when that is exceeded economy goes drastically down, hull speed is much related to the length( and also beam) of the hull.
For planning huls have mainly focus on wetted surface area. I did mention the width of the hull but never said fat. The shape of the wetted surface is much studied, if You are really interested in the topic, google for Daniel Savitsky, a lot of the paper on the subject relies on his studies in the 1960 and later also. Weight and aerodynamics are critical for planning huls.
If we move closer to our own vessel size look at this video. Its a 4 HP outboard on a old design (out of memory 2.4 m X 1.2. Looking at the wake, it moves pretty fast, probably 13+ knots. Pitch of prop probably restricts the speed. Very flat and rather wide would say(width 50% of length).
And
Not saying this is optimal( design is from type 1950) but still the relative wide body works pretty well, dont You think? Have understood on this type of boats You can com close to 20 knots with a 5HP, that is probably possible also for a long and narrow but rather though and unpractical?
What makes me turn? The only thing i can do when standing rather statically is to move my Center of Gravity (COG) out of the Center of Buoyancy (COB), thereby tipping the surfboard to one side. Thereby the centre of lateral moves to the side, while the motor underwater tips to the opposite side. This delivers a lever so the whole board turns around the vertical axis more or less.
I agree a shorter board can be turned easier when (wind)surfing but this requires much more dynamic action, using my bodies mass inertia to lift and turn the bow and bring it down again. This is not possible with such a long board with the batteries installed in front of me.
Instead i am thinking about a longer fin, so the motor tipping out of the center would contribute more to the inbalance.
Whatâs the length of you board? Ideally what you want is a tunnel board for the motor. That way the motor sits higher up and acts less like a pendulum. You want a fin either side of the motor. I also wouldnât ride a board longer than 6ft. It becomes very hard to turn at higher speed.
Thanks for the update!
My board length is around 340cm.
I can imagine there are reasons for this kind of design, could you please explain why you would choose it? Do you have experience with such design?
Here is a pic of a tunnel hull.
As you can see the prop sits a lot closer up to the hull. It kind of sits between a jet and inboard. It provides much better handling when turning as the prop stays more centered instead of shifting side to side like a pendulum. Waterwolf use this method on their boards too:
Your board is also incredibly long! It would be very interesting to see how short you can go and still get similar speeds but with much better handling.
I have been considering a propeller tunnel hull om my motor surfer project. One of the advantages is the shallow draft. Another reason on bigger boats (inboard engines) is that the shaft angle can be kept more favorable in relation to keel line. In our application a duct can probably be integrated in to the hull shape rather easily, like Waterwolf. However my plan is to keep the motor inside the hull. I have no idea how prop tunnelwill affect handling/steering on a surf board, in some respect would imagine the tunnel would stabilize the the stern like a keel due to the denser water flow around the propeller, good or bad for turning donât know.
Again if keeping as comparison bigger boat applications usually the propeller tunnel boats(at least those i have been studying) is usually on semi displacement application, inboard engines, and probably more usual in twin engine applications but also in single engine use, not many used on light fast crafts. Waterwolf is the only one have seen in combination with a duct so far. Hope mine will be the second one:) Otherwise will not copy waterwolf, its not according to my own vision.
PowerGlider will not have any issues with the shaft angle as the motor is outside the hull so the angle can be adjusted easily. Usually optimal prop shaft angel is very close to the same as horizontal direction of movement, this way not much lost energy. Often shaft angle is used to trim the hull higher but then you always lose some efficiency.
Wonder considering the turnability, how would increasing the âVâ of the bottom affect handling? At lest stability would probably be harder to manage, but would also turning be more easy?