Why is it that a more powerful engine would need more propeller blades? To understand this problem, it is important to understand that a propeller must be tailored to the specific needs of an engine. The job of the propeller is to “absorb” the power produced by the engine and transmit that power to the air flow passing through the propeller disk. Thus, energy is added to the air to speed it up and generate a thrust force on the propeller blades. If the propeller and engine are not properly matched depending on the power of the engine, both become inefficient and performance suffers.
As engine power increases, the aircraft designer has a limited number of options to design a propeller capable of efficiently absorbing that greater power:
Increase the blade angle (or the pitch) of the propeller blades. In so doing, the angle of attack of the blades increases allowing the blades to impart greater energy to the air flow.
Increase the diameter of the propeller disk, i.e. make the blades longer. The blades will therefore transfer more energy by affecting a larger volume of air.
Increase the revolutions per minute of the propeller. The same amount of energy is transferred to the air but in a shorter time.
Increase the camber (or curvature) of the blade airfoil. A propeller blade is composed of airfoil shapes just like a wing is. Increasing the camber of a propeller blade creates a greater thrust force just like increasing the camber of a wing creates a greater lift force.
Increase the chord (or width) of the propeller blades.
Increase the number of blades.
Unfortunately, many of these options create more problems than they solve and are generally impractical for a variety of reasons.
Blade angle: The pitch of the blade is set by the angle that optimizes the aerodynamic efficiency of the blade. If this angle is changed, one kind of efficiency is lost in order to gain another. This tradeoff makes changing the blade angle a very unattractive alternative.
Blade length: While increasing tip speed is a significant issue (see the next point), size constraints are usually the biggest problem with this option. As the propeller size increases, the landing gear must become longer to avoid scraping the blade tips on the runway. This change has a domino effect on a number of other structural and weight issues.
Revolutions per minute: For the same propeller diameter, the blade tips travel faster and faster as the rotational speed increases. Eventually, the blade tips become supersonic where shock waves form, drag increases substantially, and efficiency plummets.
Airfoil camber: The blade airfoils are chosen for optimum aerodynamic efficiency. By changing sections, one kind of efficiency is again sacrificed for another. Increasing camber may also result in blade structural problems.
We are now left with the final two options, increasing the blade chord or the number of blades. Both have the effect of increasing the solidity of the propeller disk. Solidity simply refers to the area of the propeller disk occupied by solid components (the blades) versus that area open to the air flow. As solidity increases, a propeller can transfer more power to the air.
While increasing the blade chord is the easier option, it is less efficient because the aspect ratio of the blades is decreased resulting in some loss of aerodynamic efficiency. Thus, increasing the number of blades is the most attractive approach. As the power of engines increased over the years, aircraft designers adopted increasingly more propeller blades. Once they ran out of room on the propeller hub, designers adopted twin contra-rotating propellers on the same engine. Two good examples are the Tu-95 bomber and Tu-114 airliner. These Russian aircraft were equipped with the most powerful turboprop engines ever built, and both designs feature a total of eight propeller blades per engine.
- answer by Jeff Scott, 12 August 2001
Interesting article, good overview. Only one comment: you will not reach the speed of sound at the blade tips in water. Also, no shock waves. In air, the speed of sound is about 340 m/s and in water you have approx. 1400 m/s. What will or might happen if you increase rpm is that you will get pseudo cavitation (air release) in the water due to the pressure drop on the suction side of your profile and the thrust will decrease.
This all makes perfect sense, but what I’m interested in is blade shape and cavitation. For instance, what are the advantages/disadvantages of this blade:
vs this blade
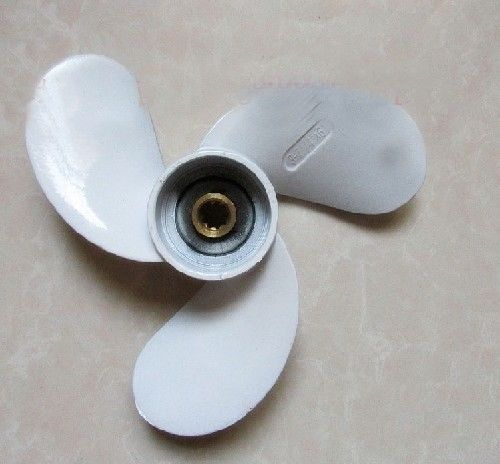
vs this blade
(used without permission)
vs other blade designs.
I know that some blades are optimized for both backwards and forwards thrust, which isn’t our problem, so I’m wondering if we could choose/design a blade that is optimized for only forward thrust, or is the above black blade exactly that?
Thank you for any insight…
(addendum) I ordered the flying fish blade and the white blade (the black one was too expensive for experimentation) When they arrive I’ll put them on a testbed and see what the thrust is for a given input.
I heard that the first white prop and the black also are used on small outboard on sub-planning boats. That shape should be good against weed…
Last prop seems a little more performance wise.
Check hi power outboard boats, light craft with very high cruise speed, those prop are more inspiring for us…