Are there any ready-made passive antenna repeaters available for sale? If not, where can I read about DIY plans?
If you have your current antennae touching the case on the inside of your compartment and your compartment is a solid material, you can simply tape an antenna extension to the outside directly over where the internal one is. That is what I did for some time with my carbon prone board that had an internal compartment.
An alternative that works even better is the following:
Vecys 2PCS U.FL IPEX to SMA… https://www.amazon.co.uk/dp/B09PTGTSY3?ref=ppx_pop_mob_ap_share
Eightwood GSM 4G LTE Antenna 3dBi… https://www.amazon.co.uk/dp/B07ZYDZYYD?ref=ppx_pop_mob_ap_share
If you can, try to find a cable that is shorter. 3m is excessive and I will cut it down and connect another SMA fitting to it.
Hope that helps.
Try Taping outside of case with a 1/4 wavelength stripped casing of antenna cable, overlap of 27-31mm
Commercially foil drive sell one for a very high price. Not hard to make though.
Well, what I decided to try is a patch antenna from the quadcopter remote control + a flexible antenna from the radio station, which I will lay under the bottom and bring to the nose. Do you think this will work?
Everything works. Today, I started for the first time on my carbon board. Due to the fact that the antenna is quite short, the start was difficult. The antenna panel under the box is not secured in any way, it is simply pressed by the body itself, the clamping force is sufficient.
I ordered a cable with an RP-SMA connector, I will lay it under the bottom and bring the antenna to the bow…
That should do the trick.
The unit looks good. Do you notice any flex in the 3D printed housing?
Surprisingly, no. Today I made quite sharp turns and did not feel that the hydrofoil was wobbly. My batteries are inserted quite tightly, perhaps this also affects the overall rigidity.
I was also pleased that the cooling turned out to be effective. I used three batteries in a row - two MAX analogues and one Sport without any symptoms of overheating.
Forgot to mention that the controller I’m using is FLYCOLOR X-CROSS 160A, which is glued with glue consisting of equal proportions of thermal paste and UHU epoxy resin to the back cover of a burnt SQESC 12200.
@rttn Thank you for details of your project!
Can you elaborate on this latch - details how to do it? It will be usefull for my above the board box project…
@Hebie
Here is a post about my order of Molicel cells from Alibaba seller. Ordered twice and will do it again.
'Foil Drive Assist, DIY - #961 by lishine
During these two days I rode a lot on the foil assist. On Armstrong carbon boards, on an inflatable board with a carbon deck, and I can say that for reliable communication you only need two small antennas from a quadcopter and a piece of cable. In the next version of the case, I make a special recess for an external antenna.
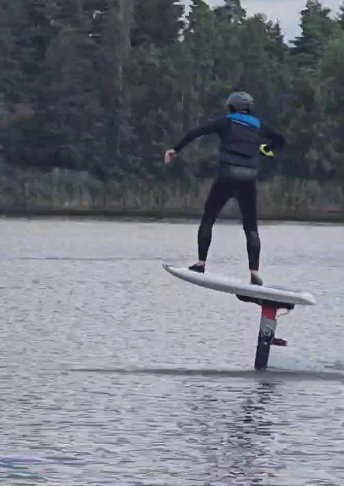
Thanks.
But the devil is in the details.
What latch you find reliable, is there really a spring, are the holders 3d printed or metal embedded or really the latch parts are screwed…
Okay, here’s the latch that’s in place now. I’ve used several different ones and haven’t found the devil other than some rusted and others didn’t. There is a spring, the latch is screwed with M3 screws to the fused brass inserts.
Thanks.
It has to be SS.
Did you consider 3d printed, like:
No, I haven’t considered it. I would definitely prefer a steel latch.
Watch the Foil Drive video on proper latch operation. Their fiberglass reinforced molded nylon latches break, and you’re talking about 3D printing…
Thanks! these FD latch videos are really useful, I didn’t know they exist!
Found some cheap with lock or with a spring on Ali and Ebay.
The silicon ring for motor connector - did you molded it or bought it?
I am also having issues with RF on carbon board and curious about your solution but I don’t quite understand— are you using both internal and external antenna with both connected to the receiver?
From what I am reading it seems that for a 3D printer, I can print in PETG, PLA or PLA+ and then wrap it in carbon. Sand it for a few hours and then it should be ready. Or outlay more for an enclosed 3D printer to print in ABS & polycarbonate.
I decided not to purchase a 3D printer during the sales because I do a fair bit of fibreglass/carbon repair and thinking about sanding 3 small foldable propellers does not interest me very much.
Foil drive used Formlabs Rigid 4000 resin for their blades and brackets.
I have seen a few threads where some people have printed in PLA+ and had no issues.
Kind of stumped. I used third-party 3D printer services before for PA12GB Glass Beads and it was on the pricey side. Has anyone had any success with a Chinese print farm with Formlab printers (any chance of sharing the contact with me)? Or advice on going ahead with a non-enclosed 3D printer and how I can print without having to wrap in carbon but still be durable enough not to constantly be checking for cracks or replacing props?
I get props and hubs printed in nylon12 by Zelta 3D in Singapore. Price is good and so are shipping rates to Australia. I don’t touch them after printing but you can lightly sand if you want.