Sorry, I am still a bit confused. I purchased a similar BMS (8S Lithium ion 15 amp discharge) and made my own battery pack. It performs the exact same as the foil drive battery and I am assuming it is working correctly and limiting the battery discharge to 15 amps. Does this mean that the ESC does not need to be such high amperage if the battery is limited to 15 amp discharge or am I missing something? Thanks.
Well 15 A will not give you enough power to lift off.
They have a separate port for charging, so i was assuming the bms is for charging only.
I mean, its inside the battery pack, but the big, xt90 cables are connected directly to the batt
As toto said, 8s at 15 amp is 500W, not even the best builds here are capable of flying at that power. So i assume it would be impossible lift of at that power.
Btw, i went to the foildrive page to see a battery pic and found they charge 65 dollars for a Y lead. Thats a 1000% markup!!
Cdubs,
I’m using the turnigy hobbyking 150Amp Marine ESC on my 6S3P and 6S4P setups.
This is similar to the Original FD system.
Discharge battery straight from the positive and negative to get full power output. Use the BMS or an external balance charger for charging the cells only.
I haven’t tried building a 8S kit due to added weight and hassle of the more expensive speed controllers or VESC needed. Pretty sure foildrive have a custom VESC for their assist plus model. It’s very compact space inside the box but their are a few off the self ESC that might do the trick.
Motor sourced direct from a supplier in China ready to go out of the box. I have a N6374 at 130kV. One issue to beware of is water tracking up inside the motor cable from the splice into the box.
I’ve been running my kit for one year and still going strong. Motor is rusting but it still goes. I’d say the life of anything immersed in salt water is limited. Great for DIY as you can easily swap out a motor or ESC if they fail or wear out. Parts for my kit totalled around $1200AUD sourced on the Internet.
A lot of hours still go into the build.
I built my first battery, but cheaper and easier to get a professional bike builder or battery supplier make custom one in my opinion.
By all means throw out the batteries if you want. The batteries are sealed from water and moisture from the factory. They have to be because they would react vigorously with the air/moisture in the atmosphere if they werent. What you need to prevent is corrosion for a longer term failure. This is not something new to electronics and extra care must be taken. I can guarantee you that those electric car batteries werent cleaned or inspected for ingress. If you have a coating to protect from corrosion and you clean the batteries appropriately after an incident there are no issues. If you dont know what “appropriately” means then you should properly dispose of said batteries. Salt is an easy compound to clean and is soluble in many solutions. Let me be very clear this is entirely different than those electric car batteries that were likely swimming in a heated salt water bath that would experience much faster corrosion rates and they were not checked for ingress or cleaned in any way and they are “sealed” battery packs. There are many things in life if you dont do proper maintenance it can lead to catastrophic consequences, doesnt mean you should throw out all the items that need maintenance.
That’s interesting. To be honest, it never occurred to me that they would be doing that. It is such an off the shelf product that I just thought they had found a cheap charger they liked with the xt30 plug and instead of changing it they just added that connection to their battery packs. I can say with 100% first hand experience that the 3 battery packs I have made so far all utilize the 15 amp discharge rate and I just paralleled the xt90 and xt30 connectors. It has the exact same performance as the foil drive batteries, same thrust, same battery life, feel the same temp after use, etc. I was actually curious what would happen if I switched to a 30 amp discharge bms because for some reason it is hard to find an 8s lithium ion 15 amp discharge bms.
It seems pretty easy to agree that a submerged battery could be risky or at least require cutting off all the enclosure to check and possibly start over. The real question is what about if just a small amount of water gets in the box (which has happened to me twice). I have made 3 batteries for my foil drive assist plus. I found it easier to just make 8S2P packs instead of 8S3P packs because the fit is so tight at that size. My first box leak actually came because I made an 8S3P that fit so tight I forced the lid to close and it didn’t seal correctly. With 8S2P there is tons of room. After the spot welding and soldering of the BMS I wrapped the entire thing in high heat tape, then wrapped the entire thing in the same wide plastic tape I use to secure the wire to the mast making sure to seal around the connectors as well as possible, then put the battery pack in a shrink wrap sleeve and use more tape to seal the ends of the sleeve. This means the battery pack is basically sealed unless it sat submerged and water found its way around the connector wires into the pack. Does anyone know of a waterproof version of the xt90? Not that I want water to get into the box but at least this way I feel it will survive if and when it happens. Foildrive coated both the ESC and remote receiver in clear epoxy so they are completely waterproof. I think anyone with foil drive type battery packs should cover the ends of the pack for an added level of safety against leaks.
Sure. It is kind of hard to see with the remote receiver on top. I can see that it says “FSESC V6.6”. When I google that it doesn’t seems to look the exact same so let me know if you find an exact match.
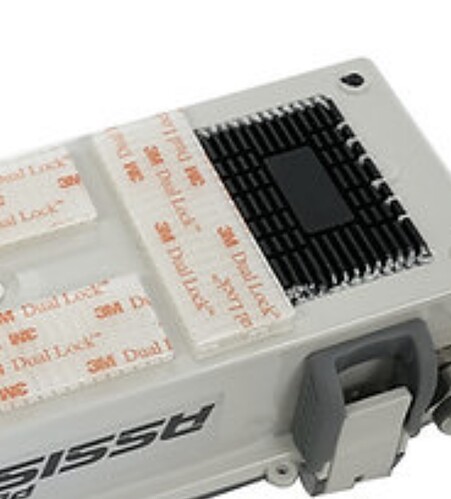
To avoid worries about salty batteries, just pot the ends of the cells in epoxy with microballons, then it is impossible for the saltwater to enter the terminals and can then be rinsed with water if enclosure has a leak. The battery will not be serviceable, but since it is few cells anyway, that is not a concern. Very easy and safe.
hi if you need info i can help you , write me in email or FB ,i think this forum dont have PM
Good job, where did u get the design files for the foldable propellers? Thx
I have been told by a robotic engineer involved with autonomous véhicule that all these batteries 18650 21700 ect have vent holes under the positive cap. They had sealed batteries pack and couldn’t figure where the condensation was coming, they discovered it was coming from the cells themselves. They are now using a kind of Goretex membrane on the pack. He also advised against potting as prevent cells to cool down effectively.
Hi all, thanks for the great info. Does anyone have a link to a Thingiverse file that I can use to order some cable mounts (see picture)? I want to outfit a couple more boards with my foildrive and although I’d love to support the official company, shipping to US it would be almost $200!
Thanks!
Most good cells have a degas cap and/or a shortcut pop cap
Meaning it is not a good idea to seal the all battery in epoxy for instant
Never seen a shortcut cap in action , but I have a few cells degas in my hand ( e-cigarette) , the cells got really hot , I had time to thrown them away and they never explosed , but that was max 2cells
Not really sure that the degas cap or vent cap works in both ways (?)
Last week I had my first dead 30Q cell , maybe + 1000cycle , IR was above 150 , and the cell just internaly shorted I guess, not heat , just went down to 0v in 2weeks
I will use it to run some test , to see if in // other cells can discharge in it …
I assume it would be a problem if it happens in a big pack and pretty hard to find out at the beginning, my only way is to check IR during charging …
Ps : all my degas cells came from external shortcut , and once it started it never stopped , the reaction was pretty high but can be handled if it’s a couple of cells … you have to do things if you allready know what to do …
Hi, i’ve slowly acquired most of the parts for my build, printer is running right now - DIY Foil Drive - Google Sheets
Last thing I need is a battery, can anyone help recommend one available ready to buy in Australia, I found a nice one on Hobbyking but the shipping was way too much when I went to buy it.
Would this one work? PMQB72006S | Prime RC 22.2v 7200mAh 100C LiPo Battery
Thanks
So after many hours of building I finally took my diy foil assist out for a spin today. A big thank you @nekitesurfing for his massive help getting me this far and patiently answering my many questions!
It worked well for 5minutes today and I experienced the potential…until I lost power and realised the motor had sheared off of the mast mount and I had lost everything…Battery box, motor and battery. I’m gutted! But not defeated, I will try again!
Next time I need to attach the battery box to the leash plug I think as a backup. Unfortunately I dont have footstraps plugs on the board as they would be an ideal secondary tie down point.
Has anyone else experienced a motor shearing off from the mount? I printed the pod at home using PETG with 80% infill. On reflection there is a lot of weight from the motor putting a lot of torsional force onto the end of the motor pod which is only thin plastic.
The photos below show the damaged motor pod after the session…
T