Thanks, that’s the size I want to use at least in my box. I might use bigger hose between the mast and the box.
@MAC would you be willing to share your Trampa board XML config file?
Also, were you able to get the voltage, amps, RPMs from the Trampa VESC to the Maytech remote instead of via the receiver?
Thanks
I am running the motor configuration exactly how the Wizard tool set it up. I did not even know there is something called a XML config file. The VESC worked right from the start. Tonight was the first time I looked at the parameters. I have more questions.
Yes it was easy to get the VESC information to the remote receiver.
If I remember correctly. The yellow (TX) and green (RX)wires shown in the photo run down to the receiver board. They connect TX—>RX, and RX–> TX. I think I recall you have to configure the remote to use the VESC data.
I finally got around to trying the duct. I did not like it. As soon as I took off I could feel the difference. I felt and heard more noise coming from the motor. Normally it is very quiet and smooth feeling. Normally I fly at about 55% on the throttle. I estimate I was at about 65% for the same performance with the duct.
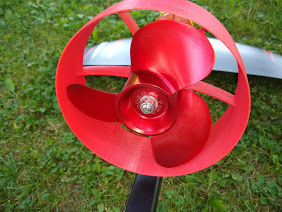
Yeah! You can definitely feel the difference when riding with a duct vs no duct! However, you will also feel the difference if you fall on the spinning prop…
After I took the ride with the duct. I removed the duct and put it in the back seat of my truck. It got too hot in the truck and the PLA plastic got deformed.
You have a lot wood for next builds
Good point. But rotted willow would not be my first choice.
Duct looks quite far from the prop. Shouldn’t they be much closer or else you aren’t getting the benefits of the duct.
Hi Mac
I’m curious about this previous power supply battery pack you referred to.
Did this not work out?
You seem to have used a more conventional pack by the end of build.
Seems like it could be a easier way to put a battery together.
Kudos build looks great.
Is anyone actually seeing a benefit from using a duct? Other than it may help from a safety stand point. I did not model the duct. Your correct there is some additional clearance.
The battery charger is working great. I will add some detail and photos next time I charge. That should be Sunday if all goes as planned.
I just went for my first ride of the season. It went well. When I went to charge the battery I found about a cup of water in the enclosure. from the looks of things It is possible that this is not the first time water reached the VESC.
Does any one know what those 3 damaged components in the bottom left corner of the top photo are?
It is direct FETs (type should be written on it), unfortunately, some of your solder pads burned so it is probably not repairable.
There are some chinese 75300 clones called 75200 which are cheaper than the original 75300. Some of these worke fine, others failed under load because of a production issue.
I got one from HGL-Tech, it works reliable so far but it is sold out. It is identical to the maker-x HI300 which is still available. It runs the 75300v3 Firmware.
How well does it work?